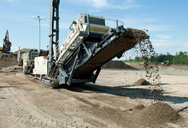
Effect of Slurry Density on Load Dynamic and
2012年4月17日 The main outcomes of the work that has been performed are: the highlight of an optimal pulp density leading to optimal mill
learn more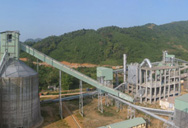
Should the slurry density in a grinding mill be adjusted as a
2007年7月1日 The increase of slurry density from 50% to 70% solids improves size reduction as well as the use of balls of smaller size. The effect of slurry density is fairly
learn more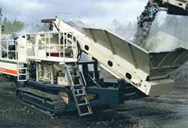
Slurry density effects on ball milling in a laboratory ball mill
1989年12月1日 We investigated the effects of slurry density, grinding time and grinding energy on the grindability of a typical platinum ore in a tumbling ball mill on a laboratory
learn more
Real-time slurry characteristic analysis during ball milling
Ball milling was performed to prepare a slurry by mixing Al 2 O 3 (99.9%, D50: 0.43 μm, AES-11, Sumitomo Chem, Japan) and deionized water (DIW) with a dispersant (5468CF,
learn more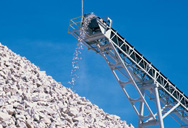
Effects of filling degree and viscosity of slurry on mill load ...
2011年10月1日 The general behaviour of a laboratory mill was explored with focus on slurry pool. Media charge orientation is not substantially affected by the presence of
learn more
Should the slurry density in a grinding mill be adjusted as a
2007年7月1日 The slurry density or pulp percentage of solids and the size of the grinding media are often considered for ball mill optimization. Laboratory grinding tests were
learn more
Slurry density effects on ball milling in a laboratory ball mill
@article{Tangsathitkulchai1989SlurryDE, title={Slurry density effects on ball milling in a laboratory ball mill}, author={Chaiyot Tangsathitkulchai and Leonard G. Austin},
learn more
Effects of slurry pool volume on milling efficiency
2014年4月1日 Slurry filling U was varied from 1.5 to 3.0 with reference to 20% ball filling. Equal masses of slurry were also used for a 30% ball filling which made slurry filling U
learn more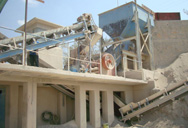
Ball Mill - On-line Estimation of In-mill Slurry Density.
2023年9月1日 Effect of Slurry Density on Load Dynamic and Milling Performances in an Iron Ore Ball Mill - On-line Estimation of In-mill Slurry Density. Bernard de Haas*#, Alfred
learn more
Effects of filling degree and viscosity of slurry on mill load ...
2011年10月1日 Ball filling and mill fractional speed were kept constant respectively at 20% and 60% while slurry filling was varied from 0% to 300%. Using a high speed video
learn more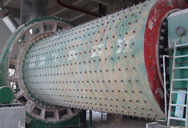
Acceleration of particle breakage rates in wet batch ball milling ...
The effect of slurry density on breakage parameters of quartz, coal and copper ore in a laboratory ball mill C. Tangsathitkulchai L. G. Austin Materials Science, Engineering
learn more
Effect of Slurry Solids Concentration and Ball
2014年3月2日 3.1. Industrial Ball Mill The ball mill utilized in the sampling survey has an inside diameter of 7.3 m and length of 9.6 m and is run in open circuit. Under normal operating conditions, the mill ball loading is
learn more
Should the slurry density in a grinding mill be adjusted as a
2007年7月1日 The slurry density or pulp percentage of solids and the size of the grinding media are often considered for ball mill optimization. Laboratory grinding tests were conducted to identify possible ...
learn more
The Effect of Grinding Media on Mineral Breakage Properties
2021年12月11日 The mill uses a laboratory hammer-shaped ball mill, and 500 g of mineral samples and 300 g of water are uniformly taken each time with the slurry concentration being 62.5%. The fineness tests were carried out using steel balls of 8 different sizes in laboratory for different grinding periods.
learn more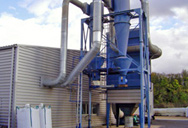
Experimental study and numerical simulation of the influence of ball ...
2023年1月1日 In the ball milling and spray drying process, the raw materials were mixed with water, binder, and dispersant in the ball mill at high speed. The raw materials, especially the carbonaceous material, were completely mixed and dispersed, and the mixed aqueous slurry was transferred through a high-pressure plunger pump to the pressure-type nozzle
learn more
Optimization of Solids Concentration in Iron Ore Ball Milling
2019年6月18日 Important advances have been made in the last 60 years or so in the modeling of ball mills using mathematical formulas and models. One approach that has gained popularity is the population balance model, in particular, when coupled to the specific breakage rate function. The paper demonstrates the application of this methodology to
learn more
A study on the effect of parameters in stirred ball milling
1993年1月1日 In this paper, four im- portant parameters of the Drais stirred ball mill, i.e., the bead density, slurry density, mill speed, and the effect of dispersant were selected for investigation. The experimental work was based on a facto- rial design and 27 milling tests were conducted. It is found that the bead density has an optimum value of 3.7 g ...
learn more
Mixing methods for solid state electrodes: Techniques,
2023年5月15日 Excellent reviews have been published summarizing the state-of-the-art in wet-based [10] or dry [11] slurry preparation, production engineering and production scenarios for the fabrication of -SSBs [12], slurry characterization, coating and drying [13], fundamentals of planetary ball milling for SSB, [14] and the processing techniques
learn more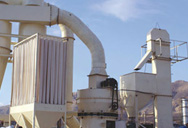
Study of the process of stirred ball milling of poorly water
2010年2月20日 The ball mill used was a Dynomill and the grinding medium consisted of zirconium oxide beads. The product is a poorly water-soluble organic compound. Laser diffraction was used to analyze the particle size distribution. ... Gao et al. [4] investigated the mill speed, the slurry density, the grinding media density and the dispersant ...
learn more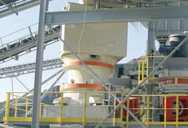
Measuring Density in Grinding Circuit - Rhosonics
If the cyclone keeps returning ore to the ball mill, the total volume of ore will be increasing in the grinding circuit. As is the density of the slurry. The recirculating ore is also called the circulating load. If the grinding process
learn more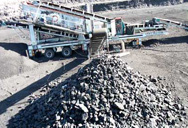
Experimental Study of Operational Parameters on
2021年12月14日 Slurry density 1340, 1460, 1610, 1790, and 2010 kg/m3 Slurry filling (U) U=0.5 - 2.5 (as volume fraction of ball bed voidage) The feed of the mill is copper ore with the size smaller than 25.4 mm, which 80 and 50 of them are 12.7 and 8 mm, respectively. The slurry concentration used in the tests was 40%, 50%, 60%, 70% and 80%.
learn more
On the analysis of fine wet grinding in a batch ball mill
1996年9月1日 The influence of the slurry density on the fine wet grinding performances of a batch ball mill was examined for an alumina hydrate feed. Irrespective of the operating conditions, the size reduction process proceeds fast in the first period of grinding (20 min); then its rate progressively reduces and after 1–2 h the size of the product approches a
learn more
(PDF) DESIGN AND FABRICATION OF MINI BALL MILL
2016年3月25日 [22] Effect of Slurry Density on Load Dynamic and Milling Performances in an Iron Ore Ball Mill - On-line Estimation of In-mill Slurry Density Bernard de Haas, Alfred V an den Bosch, Axel Köttgen
learn more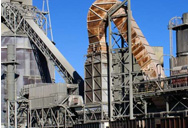
Ball Mill - On-line Estimation of In-mill Slurry Density.
2023年9月1日 Comminution Conference 2012 – Cape Town 1/9 Effect of Slurry Density on Load Dynamic and Milling Performances in an Iron Ore Ball Mill - On-line Estimation of In-mill Slurry Density.
learn more
Characterization and performance analysis of silicon carbide ...
2002年4月20日 The pH of the SiC powder dispersed in de-ionized water is about 6.5. Addition of 13 wt.% PTFE increased the pH of the slurry to about 7.4.The results of the zeta potential measurements at various pH values of the slurries prepared by ball milling and mechanical stirring are shown in Fig. 2.The experimentally observed iso-electric point
learn more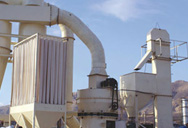
(PDF) Determination of the formal powder filling of a wet ball mill
2019年1月1日 In terms of supporting data, total mass content, ball filling, slurry density, load orientation, power draw, and material transport through the mill were measured under various conditions.
learn more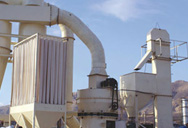
Comprehensive effort on electrode slurry preparation for
2020年12月31日 The effect of ball milling on properties of the electrode can be gauged through rheological characteristics of the slurry. We have measured shear stress, σ, versus shear rate, γ ˙, at steady state for both types of slurries (BM-S and WBM-S) and their precursor slurries and solutions as shown in Fig. 1 a. Both slurries contain 24.1% w/w
learn more
Effect of ball size and powder loading on the milling efficiency
2013年12月1日 The particle size reduction results from the complicated dynamic interaction of the balls with turbulent slurry during the ball mill process, imposing a difficulty in quantitative interpretation of the observed phenomena of: (1) the existence of the optimized ball size at a given rotation speed; and (2) the decreased optimum ball size
learn more
Optimization of Solids Concentration in Iron Ore Ball Milling
2019年6月18日 Important advances have been made in the last 60 years or so in the modeling of ball mills using mathematical formulas and models. One approach that has gained popularity is the population balance model, in particular, when coupled to the specific breakage rate function. The paper demonstrates the application of this methodology to
learn more